HULK Metal has an ISO 9001-certified lost foam casting factory and a complete supply chain to provide excellent services. Kindly contact our sales manager for more suitable solutions and more competitive prices.

As an Excellent Lost Foam Casting Company
Supply Better Lost Foam Casting OEM Service
-
Advantages
-
Capacities
-
Processes
-
Parts
-
Types
-
Foundry
-
Introduction
-
Articles
-
Review
-
Top
WHY CHOOSE HULK METAL LOST FOAM CASTING?
HULK Metal's lost foam casting plant can complete castings with a maximum unit weight of five tons and can produce marine transmission equipment casings. After vertically integrating the supply chain, we have the ability to provide better OEM services. We are your best choice. Kindly contact us to get a quote.
-
Foundry:
We continue to integrate the lost foam foundry horizontally and can cast castings up to 40 tons currently. The factory strictly implements ISO 9001 certification. Strict production management can ensure higher product quality and shorter order lead time. You can contact the sales manager to visit the factory online or on-site.
-
Experience:
We have produced marine transmission equipment boxes, reducer boxes, large pump motor housings, substations heat sinks, etc. Our rich experience allows us to develop complete production solutions based on drawings and requirements to ensure that orders can be completed faster, with higher quality, and at a lower cost.
-
Quality:
We take the quality of every product seriously. In order to meet customer requirements, we have established a professional quality inspection team equipped with advanced testing instruments to complete the shape, tolerance, surface accuracy, hardness, and various mechanical properties of castings. We will attach material and finished product test reports to every order.
-
Service:
Through continuous integration of the supply chain to improve the entire service process to the same level. When you choose HULK Metal to complete your order, you will have a dedicated technical, production, quality inspection, design, freight, and after-sales service team led by a professional and rigorous sales manager to connect with you.
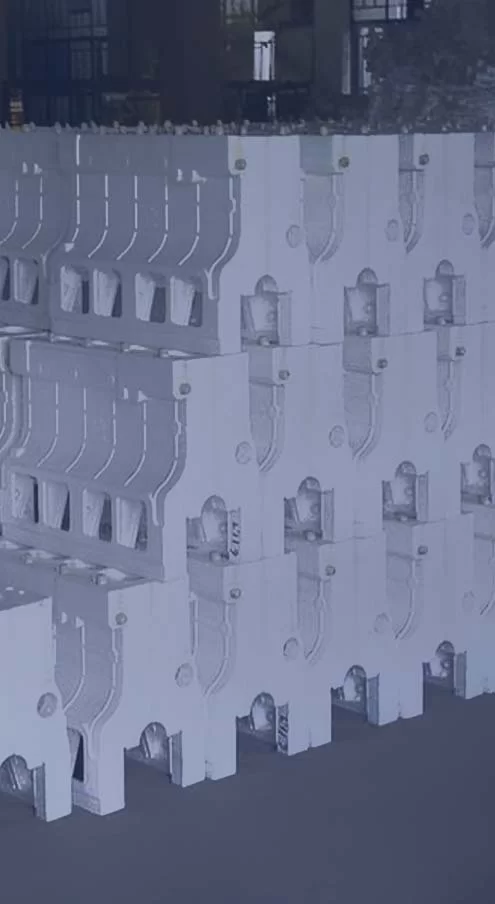
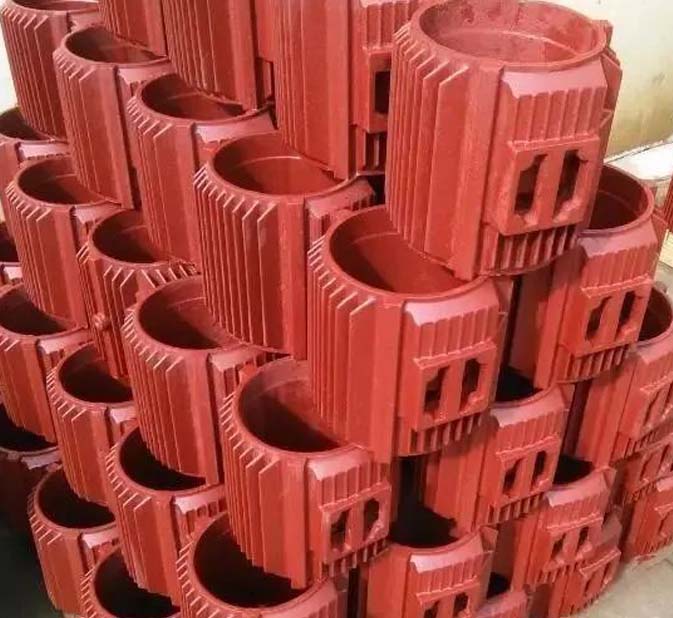
LOST FOAM CASTING SERVICES CAPACITIES
Here, we list the service form, the materials that can be cast, the single-piece weight of the casting, the minimum order quantity, etc. Through this form. You can quickly learn about our lost foam casting capabilities. Kindly contact our engineers to learn more if there is nothing here that you want to know.
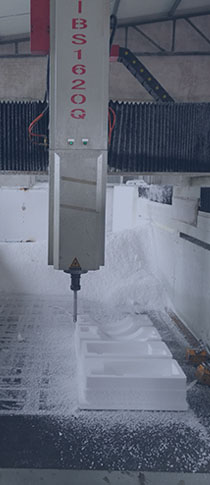
MANUFACTURING: | According To the Drawings Or Samples |
SERVICE METHOD: | OEM |
MATERIALS: | Ductile Iron, Gray Iron, Malleable Iron, Carbon Steel, Stainless Steel, Aluminum and Its Alloy |
PROCESS: | Sand Casting, Investment Casting, Lost Foam Casting, Metal Mold Casting |
WEIGHT: | <=30 Tons/piece |
PRODUCTION CAPACITY: | 1000 tons / month |
CERTIFICATION: | ISO 9001 |
FINISHING: | CNC Machining, Surface Treatment |
MOQ: | 500KG / A Standard Tray |
PROCESS OF LOST FOAM CASTING
Below is a description of our lost foam casting process and how your order is produced. Due to space limitations, we can only briefly describe it. Kindly contact our engineers if you would like to learn more. They will customize a complete solution and quote based on your requirements and drawings.
-
01
Customize Solutions
First, we customize a complete solution according to the drawings and other requirements and reduce costs as much as possible while ensuring order quality and on-time delivery.
-
02
Model Making
Model production can be done by cutting foam plastic or using foam particles to fill the mold. Complex castings may require several parts of the model to be made and then assembled together.
-
03
Refractory Material Coating
Brush or spray refractory material on the surface of the manufactured Model and dry it.
-
04
Sand Filling
Place the special sandbox on the three-dimensional shaking table. After vibrating and smoothing the bottom sand, put in the Model coated with refractory material. Continue to pour in sand and tap it flat.
-
05
Pouring
During pouring, the entire system is under negative pressure. The liquid metal can fill and shrink better, and the density of the casting can be improved. Castings can be cast in a fretting state to obtain special metallographic phases.
-
06
Metal Smelting:
The raw materials that can be processed by lost foam casting mainly include gray cast iron, non-ferrous alloys, ordinary carbon steel, ductile iron, low carbon steel, and alloy steel. Different metals need to pay attention to the moment when ingredients are added during the smelting process.
-
07
Cooling And Cleaning:
Cooling, shaking out, cutting gates, cleaning the surface of the casting, you can get the desired semi-finished product or finished product. Some castings also need to undergo heat treatment, machining, and surface treatment after completing the step.
-
08
Heat Treatment:
Whether heat treatment is required depends on the application of the casting. If the casting needs to bear the load, have corrosion resistance, and have processability, solution treatment, quenching, or aging treatment is required.
-
09
Finishing
Metal castings with higher precision requirements also require machining to adjust surface accuracy, tolerances, etc. Surface treatment methods such as electrophoresis, passivation, and spraying make castings more beautiful and corrosion-resistant.
-
010
Quality Control
Our quality control center can and will test the metallography, hardness, surface accuracy, and mechanical and chemical properties of castings. We will issue detailed material and product testing reports upon request.
-
011
Packaging & Delivery:
We can customize packaging materials and provide packaging printing and other services. We have a professional freight consultation center to help you find a more suitable freight company when you need it.
-
012
After Service
After the order is delivered, we will ensure the quality of each product through complete after-sales service. We have developed a whole return, replenishment, exchange, and policy. Kindly contact our sales manager for details.
METAL PARTS WE PRODUCED
Here, we show parts completed using lost foam casting, such as reducer casing, pump body, valve body, marine castings, etc. We will provide complete solutions and high-quality quotations based on the drawings. Kindly contact our sales manager to get them.
More Results
LOST FOAM CASTING TYPES WE CAN USE
Lost foam casting is mainly classified according to the material of the model, production method, casting material, etc. The following is the lost foam casting process classified according to pattern making.
Gray Iron Lost Foam Casting
Ductile Iron Lost Foam Casting
Steel Lost Foam Casting
-
Gray Iron Lost Foam Casting
The grades of gray iron include HT100, HT150, HT200, HT250, HT300, and HT350. These gray irons can all be produced using lost foam casting. Because of the particularity of the lost foam casting process, the pattern can be made very large and can be used to produce large castings up to 40 tons. Therefore, we use lost foam casting to manufacture pump bodies, valve bodies, boxes, marine castings, etc. Large castings. Because its pattern production process is more complicated than investment casting and sand casting, it is more suitable for small orders.
-
Ductile Iron Lost Foam Casting
The grade composition of ductile iron is QT (ductile iron), 400 (tensile strength 400MPa), 17 (elongation 17%). Each country has a specific representation. A grade comparison table is needed to better find materials. The casting performance of ductile iron is only better than that of steel, and it can replace steel in some cases. Lost foam casting can be used to cast medium and large valve bodies, pump casings, reducer casings, medium and large motor casings, marine transmission cases, etc.
-
Steel Lost Foam Casting
The surface accuracy range of lost foam casting steel parts is Ra3.2 to 12.5μm, the dimensional accuracy is CT7 to 9, and the machining allowance is 1.5 to 2mm. This can greatly reduce the cost of machining and reduce the processing time by at least 40% compared to sand casting. When choosing lost foam casting or investment casting, the weight of the steel casting is mainly considered. When the weight of a single piece exceeds 40KG, it is recommended to choose lost foam casting. Our team will select the appropriate casting process according to your needs, develop a complete solution and calculate a more competitive price. Kindly contact us to get them if you have an order for steel castings and need OEM.
VISIT LOST FOAM CASTING FOUNDRY
We welcome everyone to visit our lost foam foundry because we are proud of it. It has complete production equipment, a quality control center, and an experienced team. So we can complete orders for castings of most materials. Kindly contact our sales manager. They will take you to visit it Online or Onsite.
-
Lost Foam Casting QC Center
Control the quality of the entire order by inspecting raw materials, semi-finished products, and finished products. Can issue material and finished product testing reports upon request.
-
Advanced Lost Foam Casting Line
The advanced lost foam casting line can complete the production of each order more efficiently and with high quality.
-
Lost Foam Casting Team
Be able to skillfully operate and maintain production and testing equipment to ensure the efficient execution of each process.
LOST FOAM CASTING INTRODUCTION
We have compiled some knowledge about Lost Foam Casting to help customers understand it better. Here are the definitions of lost foam casting, its advantages and disadvantages, what castings it can be used to produce, etc. We have also listed some of the benefits you will receive from having your castings manufactured by us. Kindly contact us for details.
-
Lost Foam Casting Means:
Lost foam casting uses foam plastic to make a casting model. After applying refractory material, use a vibration table to complete the mold without taking the model out. The metal pouring is completed under negative pressure, followed by cooling, cleaning, and finishing to complete the casting process.
-
Advantages Disadvantages and Application:
Advantages: The surface roughness of castings can reach Ra3.2-12.5 μm, and the dimensional accuracy can reach CT7-9.S, which has high production efficiency and low cost. Can cast various castings with complex shapes and large sizes.
Disadvantages: Each casting has a unique shape and is not recyclable. The overall strength of the casting is slightly lower than that of traditional castings.
Applications: automotive engines, chemical equipment, marine engineering equipment, machine tools, molds, precision instruments, transmission equipment, parts for ships and other equipment
WHAT YOU WILL GET CHOOSING OUR LOST FOAM CASTING SERVICES.
Save more energy and time costs; higher product quality, faster order completion, and delivery; complete quality assurance services. Kindly contact our sales manager for details. He will lead a team to deliver exceptional service.
ARTICLE OF LOST FOAM CASTING
Here, you will find some things that we haven't covered in detail on this page. And in addition to what we have stated above. Kindly contact our sales manager for the latest quotation and a more suitable solution if you have castings that need OEM.