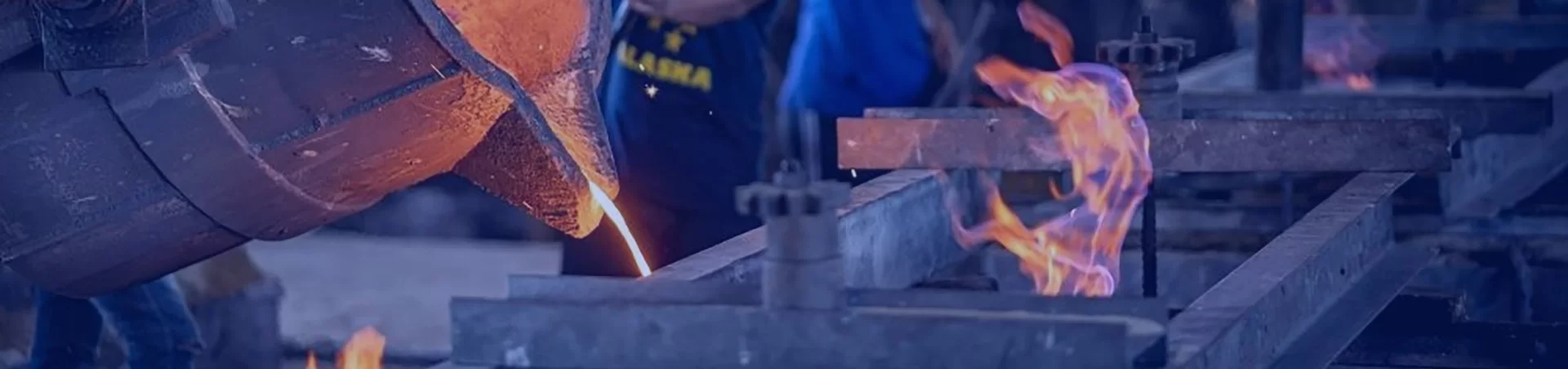
Understanding Tolerance and Allowance in Casting: Key Concepts for Precision and Quality
-
Home>
-
Blog>
-
Technology>
Understanding Tolerance and Allowance in Casting: Key Concepts for Precision and Quality
In the world of metal casting and precision manufacturing, tolerance and allowance are more than just technical jargon - they are critical parameters that directly impact product quality, production cost, and functional performance. Whether you're producing sand castings, investment castings, or die cast parts, a solid understanding of these concepts is essential to achieving a reliable and cost-effective manufacturing process.
This article will explore the definitions, differences, and significance of tolerance and allowance in casting, along with practical tips on how to apply them in real-world scenarios.
What Is Tolerance in Casting?
Tolerance refers to the permissible variation in a dimension or physical property of a manufactured component. In the casting industry, it defines the acceptable range within which the actual dimensions of a cast part may deviate from the specified nominal dimensions.
For example, if a part is specified to have a diameter of 50.00 mm with a tolerance of ±0.50 mm, any part with a diameter between 49.50 mm and 50.50 mm will be considered acceptable.
Types of Tolerances in Casting:
Dimensional Tolerance - Deals with length, diameter, and thickness deviations.
Geometric Tolerance - Relates to shape, flatness, perpendicularity, etc.
Surface Finish Tolerance - Specifies the acceptable level of surface roughness or smoothness.
In metal casting processes, such as sand casting or investment casting, tolerances are influenced by various factors including:
√ The complexity of the part geometry
√ The material being cast (e.g., aluminum, steel, ductile iron)
√ The casting method and tooling used
√ Shrinkage rates and cooling behavior
Understanding and controlling these variables is vital for achieving consistent casting tolerances.
What Is Allowance in Casting?
Allowance, on the other hand, is an intentional dimensional adjustment made to a pattern or mold to accommodate expected changes during the casting process. Unlike tolerance, which accounts for unintentional variations, allowance is a deliberate design decision.
Common Types of Casting Allowances:
Shrinkage Allowance - Accounts for the natural contraction of metal as it cools and solidifies.
Machining Allowance - Provides extra material that can be removed during post-casting machining to achieve precise dimensions or surface finish.
Draft Allowance - Allows for easy removal of the pattern from the mold by tapering the vertical surfaces.
Distortion Allowance - Anticipates and compensates for warping or deformation during solidification.
For instance, if a steel part is expected to shrink by 2% during cooling, the mold cavity must be made 2% larger to ensure the final product meets the design requirements. This is a classic example of applying a shrinkage allowance in steel casting.
Tolerance vs. Allowance: Key Differences
Feature | Tolerance | Allowance |
Purpose | Handles unintentional variations | Handles intentional dimensional changes |
Application Stage | Inspection and quality control phase | Design and pattern-making phase |
Expression | Usually as ± deviation | Added/subtracted to dimensions |
Impact on Casting | Affects reject rate and precision | Affects pattern design and mold size |
Understanding the distinction helps foundries and engineers optimize both the pattern design and post-casting processes, thereby improving both quality and productivity.
Why Tolerance and Allowance Matter in the Casting Industry?
Improved Product Quality
Correct tolerance specifications reduce the risk of part rejection, ensuring that cast components fit and function properly in assembly. This is particularly important in industries like automotive casting and aerospace casting, where dimensional accuracy is critical.
Cost Efficiency
Overly tight tolerances can lead to increased machining time, higher tooling costs, and more scrap material. Similarly, improper allowance calculations may cause undersized or warped parts. Balancing tolerance and allowance helps maintain cost control without compromising quality.
Enhanced Manufacturability
By incorporating correct allowances into the design phase, foundries can minimize rework and avoid costly design changes later in production. This is especially important for custom casting services, where one-off or low-volume runs require upfront precision.
Best Practices for Managing Tolerance and Allowance in Casting
Collaborate Early - Encourage close communication between designers, pattern makers, and foundry engineers to ensure realistic tolerances and allowances are defined from the start.
Use Industry Standards - Refer to established standards such as ISO 8062 or ANSI for general casting tolerances based on part size and process.
Account for Post - Casting Processes - Include machining allowance if post-processing (e.g., CNC machining) is needed for critical surfaces or tight fits.
Choose the Right Casting Method - Processes like investment casting can achieve tighter tolerances compared to sand casting or shell molding. Select the method that aligns with your accuracy needs.
Utilize Simulation Software - Modern foundries use casting simulation tools to predict shrinkage, deformation, and other behaviors, improving allowance planning accuracy.
Final Thoughts
In summary, tolerance and allowance are foundational elements in the successful production of high-quality cast components. While tolerance defines the acceptable range of variation, allowance accounts for the expected changes during the casting process. Both need to be carefully calculated and managed to ensure dimensional accuracy, minimize costs, and enhance overall manufacturing efficiency.
Whether you're working with ductile iron castings, aluminum gravity castings, or complex custom cast parts, mastering these two concepts can set your business apart in a highly competitive industry.
Need Expert Help with Casting Tolerances and Allowances?
Our engineering team at Hulk Metal specializes in precision casting services tailored to your requirements. From concept to finished part, we help you balance design goals with manufacturing realities. Contact us today for expert consultation and high-quality castings you can trust.
Article Navigation
Article Navigation
Industries
Foundries
-
April.23, 2025
How to Find A Cost-Efficient Metal Casting Manufacturer?
READ MORE
-
March.28, 2025
Everything You Need to Know About Die Casting!
READ MORE
-
March.26, 2025
Sand Casting vs. Die Casting: Which is Right for Your Project?
READ MORE
-
March.25, 2025
CNC Cutting vs. Laser Cutting: Which One is Right for Your Project?
READ MORE
-
March.03, 2025
Addressing Defects in Castings: A Comprehensive Guide
READ MORE