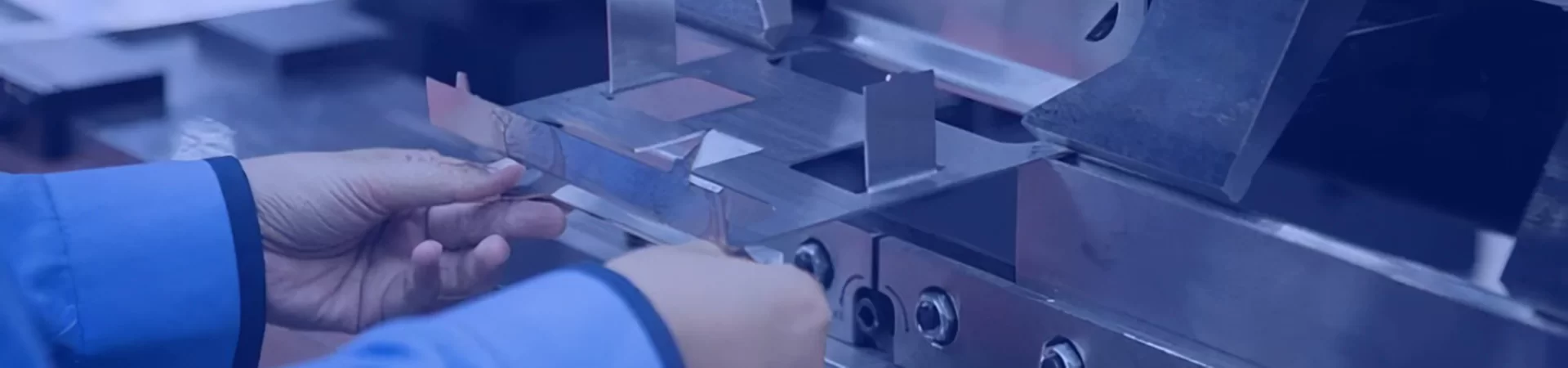
Something You Need to Know About Sheet Metal Fabrication
-
Home>
-
Blog>
-
Technology>
Something You Need to Know About Sheet Metal Fabrication
In today's world of manufacturing and industrial production, sheet metal fabrication plays a pivotal role. Whether you're building components for aerospace, enclosures for electronics, or custom parts for the automotive or construction sectors, sheet metal and its precise fabrication processes are indispensable. This article aims to provide a comprehensive, in-depth look at sheet metal fabrication, from the fundamentals and typical services to its real-world applications and how to choose the right supplier - ending with why Hulk Metal stands out as a reliable partner in sheet metal services.
What Is Sheet Metal Fabrication?
Sheet metal fabrication refers to the process of turning flat sheets of metal - such as stainless steel, aluminum, carbon steel, brass, and copper - into finished metal parts or structures through cutting, bending, and assembling. These processes often involve a combination of manual and automated techniques, supported by CNC machines, laser cutters, and robotic welders to ensure accuracy and efficiency.
This type of manufacturing is widely used due to its cost-effectiveness, scalability, and suitability for both prototype and large-scale production runs.
The sheet metal processing workflow typically includes:
√ Laser cutting / CNC punching for precision part separation
√ Bending and forming using press brakes or rollers
√ Welding and fastening to join multiple parts
√ Surface finishing (powder coating, anodizing, plating) for protection and aesthetics
√ Quality control to ensure dimensional accuracy and performance
Common Materials Used in Sheet Metal Work
The choice of material depends on the application requirements such as strength, weight, corrosion resistance, and aesthetic needs. Commonly used materials in sheet metal services include:
Aluminum: Lightweight and corrosion-resistant, suitable for automotive and aerospace applications.
Stainless Steel: Durable and corrosion-resistant, ideal for medical, food-grade, and outdoor products.
Carbon Steel: Cost-effective and strong, widely used in construction and machinery.
Galvanized Steel: Pre-coated with zinc for enhanced rust protection.
Copper and Brass: Excellent for electrical conductivity and decorative purposes.
Core Sheet Metal Fabrication Processes
To fully understand the value of sheet metal processing, it's helpful to break down the major steps involved:
Cutting
Cutting is the first and often most critical step. Modern sheet metal cutting services utilize:
Laser cutting: High-precision cutting, suitable for tight tolerances and complex shapes.
Plasma cutting: Effective for thicker materials and fast throughput.
Waterjet cutting: No heat-affected zones, making it ideal for sensitive materials.
Shearing or punching: Common in high-volume, repetitive part production.
Bending
This involves deforming the metal sheet to a specific angle or shape using press brakes or folding machines. Accuracy and repeatability are key in this stage, especially for components that must fit within tight assemblies.
Forming & Rolling
For cylindrical or conical parts, forming and rolling processes are used to shape the flat sheet into a 3D structure.
Welding & Joining
After shaping, components are assembled using TIG, MIG, or spot welding depending on the material and strength requirements.
Surface Finishing
Post-processing options like powder coating, anodizing, plating, or polishing are added for aesthetics, corrosion protection, or conductivity.
Applications of Sheet Metal Fabrication
The versatility of sheet metal fabrication services makes them critical across many industries:
√ Automotive: Body panels, brackets, exhaust components.
√ Electronics: Enclosures, server cabinets, heat sinks.
√ Construction: HVAC ducts, facades, framing elements.
√ Aerospace: Lightweight structural components.
√ Medical Devices: Stainless steel housings, trays, and tools.
√ Furniture: Custom metal furniture, fixtures, and accessories.
Customization and Prototyping in Sheet Metal Services
For companies seeking unique or low-volume production runs, custom sheet metal fabrication is essential. This includes:
√ Rapid prototyping
√ OEM part production
√ Design assistance and DFM (Design for Manufacturability)
√ Short turnaround times
Modern sheet metal service providers offer advanced 3D modeling and simulation tools to test and perfect designs before physical production, saving both time and cost.
What to Look for in a Sheet Metal Fabrication Supplier
When evaluating a sheet metal processing partner, consider the following factors:
Technical Capabilities: Does the supplier offer laser cutting, CNC bending, welding, and finishing in-house?
Material Expertise: Can they work with the specific material grades and thicknesses you need?
Customization Options: Are they capable of custom projects or complex assemblies?
Quality Assurance: Do they have ISO certifications and rigorous QC procedures?
Turnaround Time: Can they meet your deadlines without compromising quality?
Global Experience: Are they experienced in exporting and supporting international clients?
Engineering Support: Do they offer engineering consultation to improve part design and cost-efficiency?
The Importance of Choosing the Right Sheet Metal Fabricator
While many suppliers offer basic sheet metal work, not all are equipped to handle complex projects that demand tight tolerances, high-speed production, or customized assemblies. The right fabrication partner should offer:
√ Engineering support to optimize designs for manufacturability
√ Material sourcing capabilities for cost-effective procurement
√ Full-service production from prototype to final assembly
√ Strict quality assurance with documentation and traceability
√ Flexible lead times and scalable output to meet project timelines
Whether you are an OEM seeking a reliable long-term partner or a startup with a one-time custom requirement, selecting a capable and communicative sheet metal service provider can make or break your success.
Why Hulk Metal Is Your Trusted Sheet Metal Fabrication Partner?
If you're looking for a sheet metal fabrication company that can provide precision, flexibility, and consistent quality - Hulk Metal is ready to meet your needs.
At Hulk Metal, we understand that no two projects are alike. That's why we provide tailor-made sheet metal fabrication solutions designed around your specific needs. Our facilities are equipped with state-of-the-art CNC cutting machines, bending equipment, and welding stations—operated by a skilled team with years of experience in handling complex fabrication jobs.
From raw material selection to final inspection, every step of our sheet metal processing workflow is tightly controlled to ensure dimensional precision, structural integrity, and visual appeal. We serve a broad range of industries and can work with your drawings, prototypes, or functional specifications to deliver exactly what you envision.
Whether you need precision enclosures, custom brackets, metal cabinets, or industrial components, Hulk Metal is ready to help. Contact us today to discuss your sheet metal fabrication needs - and discover what a true manufacturing partner can do for you.
Article Navigation
Article Navigation
Industries
Foundries
-
May.07, 2025
Investment Casting vs. Sand Casting: Which Process Suits Your Project Best?
READ MORE
-
April.14, 2025
CNC Milling vs. CNC Turning: Unraveling the Key Differences for Your Project
READ MORE
-
April.09, 2025
Why Choose Hulk Metal to Customize Your Plowshare for Agriculture Machinery?
READ MORE
-
April.01, 2025
What Factors Should Be Considered When Choosing A Metal Casting Method?
READ MORE
-
March.18, 2025
Surface Roughness Comparison of Castings with Different Materials and Processes
READ MORE