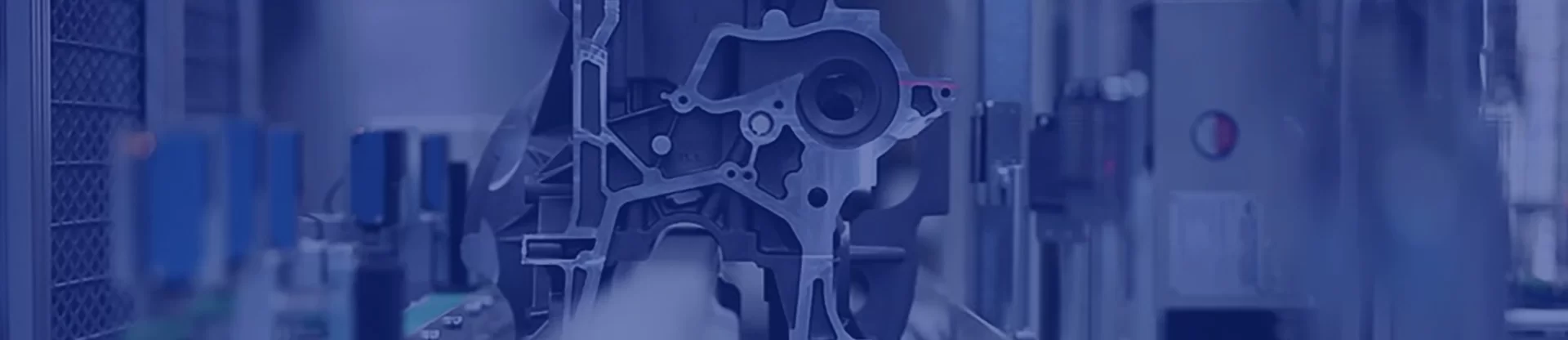
Casting Molds: The Heart of Precision Casting
-
Home>
-
Blog>
-
Technology>
Casting Molds: The Heart of Precision Casting
In the vast realm of manufacturing, casting stands as a cornerstone process, enabling the creation of intricate and robust metal components. At the very core of this process lies the casting mold, an indispensable tool that shapes molten metal into the desired form. Casting molds are not merely cavities; they are the architects of precision, dictating the final dimensions, surface finish, and structural integrity of castings.
The Basics of Casting Molds
Definition and Function
A casting mold is a hollow cavity, typically crafted from materials such as sand, metal, or ceramic, designed to receive molten metal. When the molten metal is poured into the mold, it fills the cavity, conforming to its shape. As the metal cools and solidifies, it takes on the exact form of the mold, resulting in a cast part. The mold serves as a negative impression of the final product, allowing for the replication of complex geometries with high accuracy.
Importance in the Casting Process
Casting molds play a pivotal role in the casting process, influencing every aspect of the final product. They determine the shape and dimensions of the casting, ensuring that it meets the strict tolerances required by the application. A well-designed mold can minimize defects such as porosity, shrinkage, and misruns, resulting in high-quality castings with excellent mechanical properties. Moreover, the mold's surface finish directly impacts the surface quality of the casting, reducing the need for post-processing operations.
Types of Casting Molds
Sand Molds
Green Sand Molds
Green sand molds are one of the most common and cost-effective types of casting molds. They are made from a mixture of sand, clay, and water, which is packed around a pattern to form the mold cavity. The term "green" refers to the fact that the mold is used in a moist state. Green sand molds offer good collapsibility, allowing the casting to shrink freely during solidification, which reduces the risk of cracking. They are suitable for a wide range of casting sizes and shapes and are commonly used in the production of iron, steel, and non - ferrous alloy castings.
Dry Sand Molds
Dry sand molds are similar to green sand molds but are dried before use. This drying process improves the strength and dimensional stability of the mold, making it suitable for more complex and precision castings. Dry sand molds can withstand higher temperatures and offer better surface finish compared to green sand molds. They are often used in the casting of high - quality steel and alloy components.
No - Bake Sand Molds
No-bake sand molds are made using a mixture of sand and a chemical binder that cures without the need for baking. This process simplifies mold production and reduces energy consumption. No-bake sand molds offer good dimensional accuracy and surface finish and are commonly used in the casting of medium-to-large-sized parts, such as automotive components and machinery parts.
Permanent Molds
Metal Permanent Molds
Metal permanent molds are typically made from cast iron, steel, or bronze. They are designed to be reused multiple times, making them cost-effective for high-volume production. Metal permanent molds offer excellent dimensional accuracy and surface finish, and they can withstand high temperatures and pressures. They are commonly used in the casting of non - ferrous metals such as aluminum, magnesium, and zinc, as well as some ferrous alloys. However, the initial cost of manufacturing metal permanent molds is relatively high, and they are not suitable for casting metals with extremely high melting points.
Ceramic Permanent Molds
Ceramic permanent molds are made from high-temperature - resistant ceramic materials. They offer superior thermal stability and chemical resistance compared to metal permanent molds, making them suitable for casting metals with high melting points, such as steel and nickel-based alloys. Ceramic permanent molds can also provide excellent surface finish and dimensional accuracy. However, they are more brittle than metal permanent molds and require careful handling.
Investment Molds
Investment molds, also known as lost-wax molds, are used for producing highly detailed and precision castings. The process involves creating a wax pattern of the desired part, which is then coated with a ceramic slurry. After the ceramic coating has dried, the wax is melted or burned out, leaving behind a hollow ceramic mold. Molten metal is then poured into the mold, filling the cavity left by the wax pattern. Investment molds are capable of producing castings with extremely fine details and high dimensional accuracy. They are commonly used in the jewelry industry, as well as in the production of aerospace components, medical implants, and high - performance engine parts.
Design Considerations for Casting Molds
Part Geometry and Dimensions
The design of the casting mold must closely follow the geometry and dimensions of the final part. Complex geometries may require the use of multiple mold components or the incorporation of special features such as cores to create internal cavities. The mold design should also account for any draft angles required for easy removal of the casting from the mold. Draft angles are typically small angles added to the vertical surfaces of the mold cavity to facilitate the ejection of the casting without damaging it.
Molding Process Requirements
Different casting processes, such as sand casting, die casting, and investment casting, have specific requirements for the mold design. For example, in die casting, the mold must be able to withstand high pressures and rapid filling of the cavity with molten metal. In sand casting, the mold needs to be designed to allow for proper venting of gases and the smooth flow of molten metal. The mold design should also consider the cooling rate of the casting, as this can affect the microstructure and mechanical properties of the final product.
Material Selection
The choice of mold material is crucial and depends on several factors, including the type of metal being cast, the casting process, the number of castings required, and the desired surface finish and dimensional accuracy. As mentioned earlier, sand molds are suitable for a wide range of applications due to their low cost and versatility. Metal permanent molds are preferred for high-volume production of non-ferrous metals, while ceramic molds are used for casting high-temperature metals. The mold material should have sufficient strength, heat resistance, and thermal conductivity to withstand the rigors of the casting process without deforming or cracking.
Ejection and Venting
Efficient ejection of the casting from the mold is essential to prevent damage to the part. The mold design should include provisions for easy ejection, such as ejection pins or knockout plates. Venting is also a critical aspect of mold design. During the casting process, gases are generated within the mold cavity, and if not properly vented, they can cause defects in the casting, such as porosity or blowholes. Venting channels or vents are typically incorporated into the mold to allow the escape of gases as the molten metal fills the cavity.
Manufacturing of Casting Molds
Pattern Making
Pattern making is the first step in the production of casting molds. A pattern is a replica of the final part, typically made from wood, plastic, or metal. The pattern is used to create the mold cavity by packing molding material around it. In the case of sand molds, the pattern is removed from the mold cavity before pouring the molten metal. For investment molds, the wax pattern is melted or burned out after the ceramic coating has been applied. The accuracy of the pattern directly affects the accuracy of the final casting, so pattern making requires careful craftsmanship and attention to detail.
Mold Assembly
Once the individual components of the mold have been fabricated, they need to be assembled. In the case of multi-part molds, such as split-type sand molds or complex die-casting molds, precise alignment and fastening of the components are crucial to ensure the integrity of the mold cavity. The assembly process may involve the use of bolts, clamps, or adhesives to hold the mold components together. In some cases, additional features such as cooling channels or heating elements may be incorporated into the mold during assembly to control the temperature of the casting process.
Quality Control
Quality control is an integral part of the mold manufacturing process. Each mold is inspected for dimensional accuracy, surface finish, and structural integrity. Dimensional inspections are typically carried out using precision measuring instruments such as calipers, micrometers, and coordinate measuring machines (CMMs). The surface finish of the mold is evaluated to ensure that it meets the requirements for the casting process. Any defects or irregularities in the mold are identified and corrected before the mold is put into production. Additionally, the mold may be subjected to testing, such as pressure testing for die-casting molds, to ensure its ability to withstand the forces and temperatures encountered during the casting process.
Maintenance and Repair of Casting Molds
Regular Maintenance
Regular maintenance is essential to prolong the lifespan of casting molds and ensure consistent casting quality. Maintenance activities typically include cleaning the mold to remove any accumulated residue, lubricating moving parts (if applicable), and inspecting the mold for signs of wear, erosion, or damage. In the case of metal permanent molds, periodic heat treatment may be required to restore the mechanical properties of the mold material. Sand molds may need to be re-conditioned by adding fresh sand and binder to maintain their strength and collapsibility.
Repair Techniques
When a casting mold is damaged, various repair techniques can be employed depending on the nature and extent of the damage. For minor surface defects, such as scratches or small cracks, techniques such as welding, brazing, or filling with a suitable repair material may be used. In the case of more severe damage, such as broken mold components, replacement parts may need to be fabricated and installed. The repair process should be carried out carefully to ensure that the repaired mold meets the same quality and performance standards as a new mold.
Future Trends in Casting Mold Technology
Advanced Materials
The development of new and advanced materials for casting molds is an ongoing trend. These materials offer improved properties such as higher heat resistance, better thermal conductivity, and enhanced wear resistance. For example, the use of composite materials and nanomaterials in mold manufacturing shows great potential for improving mold performance and extending its lifespan. New ceramic materials with tailored properties are also being developed to meet the demands of casting high-temperature and reactive metals.
Digital Design and Simulation
Digital design and simulation technologies are revolutionizing the casting mold industry. Compute-aided design (CAD) software allows for the creation of highly detailed and accurate mold designs. Computer-aided engineering (CAE) software, on the other hand, enables the simulation of the casting process, including the flow of molten metal, the solidification process, and the prediction of potential defects. By using these simulation tools, mold designers can optimize the mold design before manufacturing, reducing the need for costly trial-and-error processes and improving the overall quality of the castings.
Additive Manufacturing
Additive manufacturing, also known as 3D printing, is making inroads into the casting mold industry. This technology allows for the creation of complex mold geometries that are difficult or impossible to achieve using traditional manufacturing methods. 3D-printed molds can be produced more quickly and with less waste compared to conventional molds. Additionally, additive manufacturing enables the customization of molds for specific applications, opening up new possibilities for the production of small-batch and highly specialized castings.
In conclusion, casting molds are the unsung heroes of the casting process, enabling the creation of a vast array of metal components that are essential to modern manufacturing. From the humble sand mold to the sophisticated investment mold, each type of mold has its own unique characteristics and applications. As technology continues to advance, the future of casting mold design and manufacturing holds great promise, with the development of new materials, digital technologies, and additive manufacturing techniques set to further enhance the precision, efficiency, and versatility of the casting process.
For businesses seeking top-tier casting solutions, Hulk Metal stands as a beacon of excellence. As a leading professional casting manufacturer, Hulk Metal leverages its deep-seated expertise and state-of-the-art facilities to provide tailor-made casting services.
Ready to Start Your Project?
Let’s mold your ideas into reality. Whether you need prototype molds or production-grade tools, we are here to provide precision casting solutions that meet your exact needs. Contact our team today to discuss your casting mold requirements and discover how we can add value to your project.
Article Navigation
Article Navigation
Industries
Foundries
-
May.20, 2025
Something You Need to Know About Sheet Metal Fabrication
READ MORE
-
April.23, 2025
How to Find A Cost-Efficient Metal Casting Manufacturer?
READ MORE
-
March.28, 2025
Everything You Need to Know About Die Casting!
READ MORE
-
March.26, 2025
Sand Casting vs. Die Casting: Which is Right for Your Project?
READ MORE
-
March.25, 2025
CNC Cutting vs. Laser Cutting: Which One is Right for Your Project?
READ MORE